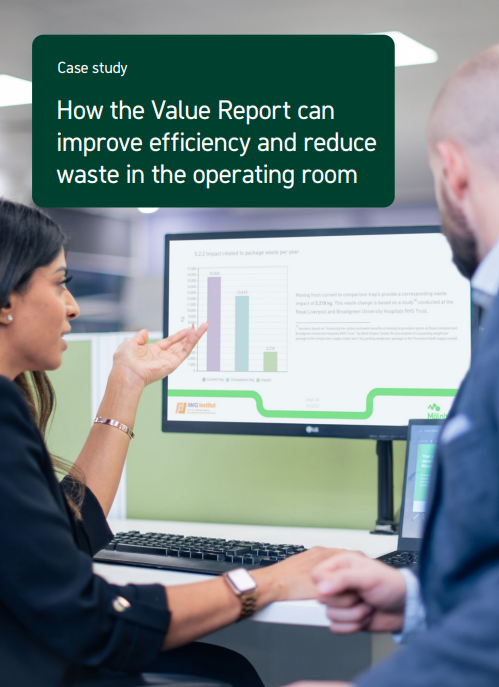
Mölnlycke has developed a digital tool to support customers in their search for improved efficiency and reduced waste in the operating room. The new Value Report tool showcases the benefits that Mölnlycke’s customised ProcedurePak® tray could bring to their operations.
Traditionally, European hospitals receive either single-packed sterile products or standard trays for surgeries. Nurses must then collect each necessary material from a storeroom and set them up individually for each procedure.
Mölnlycke has always focused on providing innovative and efficient solutions that bring value to the customer. To increase efficiency in the operating room, the company offers ProcedurePak trays containing all the necessary components required for a particular surgical procedure.
To help the customer assess the impact of using ProcedurePak trays and make informed decisions based on their specific needs, Mölnlycke has now developed the ProcedurePak Value Report.
‘The Value Report is about helping the customer make an informed decision.’ said Ivan Pretto, Business Director, Gloves & ORS, Italy. ‘The report provides three types of outcomes – a calculation of time savings, a monetary evaluation of the time savings, and a calculation of waste reduction in terms of weight and number of packages.’
The Value Report is available in both a standard and comparative version, one for single-pack and tray comparison, and the other moving from a standard tray to ProcedurePak tray.
‘The aim is to visualise the clear value of moving to ProcedurePak trays. But the driving force may differ. Efficiency or waste reduction may be critical for some whereas well-being is compelling to others. The Value Report helps customers see these aspects clearly.’ Ivan continued.
The data in the ProcedurePak Value Report is based on a study conducted by an independent party, the German Institute for Workflow Management in Health Care (IWiG), in collaboration with Mölnlycke.