Proactively managing our suppliers
With around 40 contract manufacturers and 350 suppliers to our production sites, Mölnlycke supports the employment of significant numbers of people through our suppliers around the world. We have robust programmes to ensure fair working practices and health and safety, as well as quality. Two leaders from our procurement team explain how we work to ensure ethical practices at our suppliers’ sites.
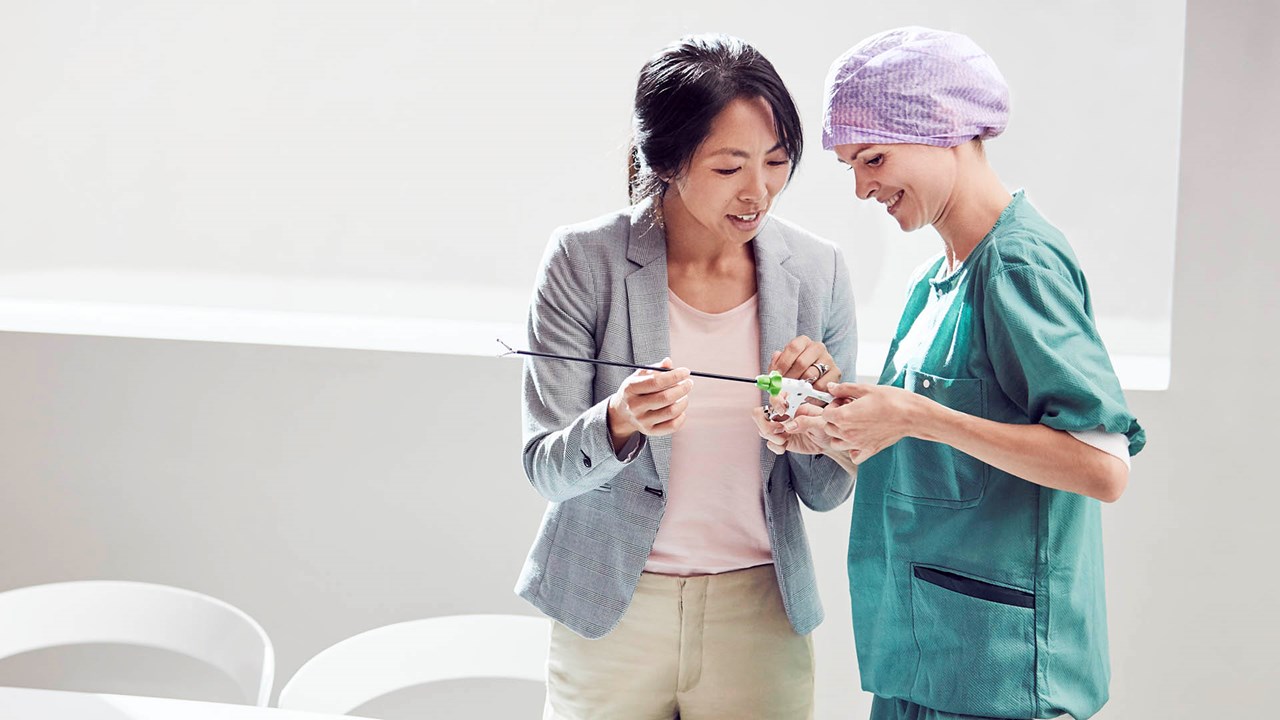
We use companies in China, Southeast Asia and North Africa as well as the US and Europe,’ says Mölnlycke’s Vice-President of Global Procurement, AnnChristine Strigén. ‘We feel a sense of responsibility towards our suppliers and the people who work there. So we have high expectations of them and we work proactively to ensure that they meet our standards.
Long-term partnerships are key to Mölnlycke’s approach. ‘The majority of our materials suppliers have been with us for more than ten years,’ she says. ‘That’s good for supply chain resilience, because the longer the relationship, the better their resources and knowledge. It also means we have been able to work with them to drive up standards over the years.’
Mölnlycke does take on new suppliers, but they undergo a very rigorous selection process, involving several audits. Contract Manufacturing Manager Gerallt Thomas explains: ‘We look at everything from people’s payslips to the security guards to how they handle their waste disposal – cross- checking our findings by interviewing employees, selected at random. Often, we use a third party with expertise in local laws and the language to help us make an in-depth assessment.’
‘If potential suppliers are too far from our aspirations, we will walk away,’ he says. ‘But if we see minor issues and they are willing to work with us to improve, we’ll move forward and develop the relationship.
’Gerallt gives an example: ‘Last year, I was looking at a supplier in Southeast Asia. We had questions over how they checked the ages of their employees. They had no intention of using child labour, but the identity documentation people were supplying could be easily forged. So we pushed them to liaise with schools and village leaders to get additional information to corroborate that potential employees were over 18.’
By partnering with businesses in this way, Mölnlycke can help them improve procedures over time and drive ethical practices.
AnnChristine explains another area in which we experience challenges: ‘Workers in certain countries and districts often want to work more than the maximum time allowed in a month,’ she says. ‘We have partnered with their employers (our suppliers) to reduce the amount of time required to do a job – perhaps by introducing automation – so they are more productive and can earn more within their existing hours.’
What next for Mölnlycke’s supplier management? ‘There will always be progress to make,’ says AnnChristine.
‘The best we can do is be proactive. We are introducing a new Supplier Code of Conduct addressing bribery and corruption, as well as working conditions and health and safety. All suppliers will have to agree to our Supplier Standard and new Code of Conduct. We’ll also be trying to influence the rest of the supply chain by asking them to get their suppliers to sign similar codes.’
This story was first published in the Sustainability report 2019.